工場移転で究極の排気対策設計!/脱臭装置なしで臭気苦情を回避した事例

-
臭気成分
海産物臭、トリメチルアミン、硫黄系臭気
-
発生場所
注染糊(ちゅうせんのり)製造/原料攪拌・加熱工程
-
導入企業
養殖用餌メーカ/製造工場
染物の糊(ノリ)を製造する工場の工場移転に伴い、移転先での臭気苦情対策に成功した事例です。
既工場ではニオイ苦情が発生していたため、移転後も発生が予想されました。事前に対策効果を確認できたカギは「臭気拡散シミュレーション」と臭気アセスメントです。
脱臭装置を導入せず低コストで対策を達成し、移転後長期にわたり苦情は発生していません。
工場移転におけるお客様のニオイ課題
移転前の既工場では専用の排気設備が無く、有圧扇での換気のみでした。
対象の原材料撹拌・加熱工程は、排出されるニオイが強く、時折、工場周辺より苦情のご連絡がありました。
移転先の工場新設予定地も近隣に住宅エリアがあるため、地域住民からの悪臭苦情が発生する可能性が非常に高いと予想されました。
しかしながら対象の製造設備は撹拌機1基であり、できるだけコストをかけずに悪臭苦情回避の対策を行いたい、というのがお客様のご要望でした。
<対策規模>
原料撹拌機: 1基(強制排気設備無し)
事例ポイント
- 工場移転計画:「新設」工場に対する設計段階でのご相談
- 既工場にて、周辺住民からニオイ苦情が発生している
- 移転先にも、近隣に住宅エリアが存在する
- できるだけ対策コストを抑えたい
- 新工場の苦情発生を、既工場のニオイ状況から予測する

新工場で苦情回避するための施策
1.現工場でのニオイ測定
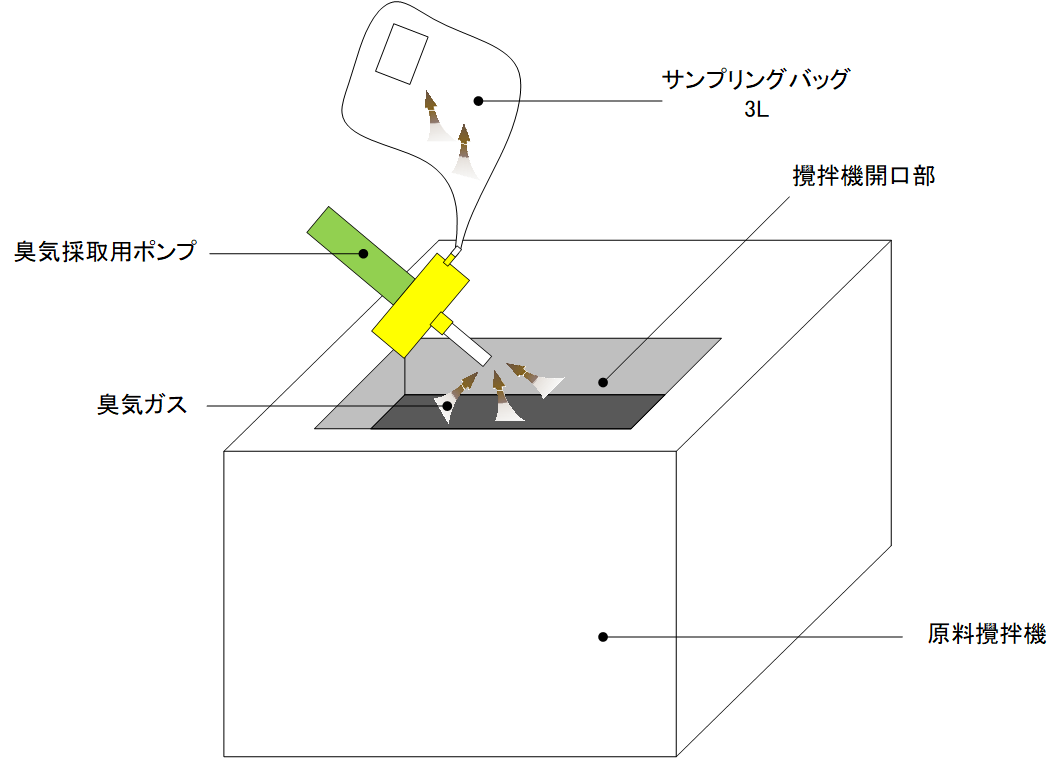
対象となるニオイがどれくらい強いのかを知るため、まずは既工場にて臭気測定を行いました。
製造工程の臭気発生源にてニオイを採取(サンプリング)し、下記の方法でニオイの強さを測定します。
測定方法
悪臭防止法に定められた測定方法であり、測定数値が人間の嗅感覚に即しているという利点があります。
実際に人間の嗅覚(鼻で嗅ぐ)を用いてニオイの強さを測定するため、悪臭苦情を対策する際には、成分濃度測定(単ガス測定)よりも有用な指標となります。
三点比較式臭袋法により、臭気指数・臭気濃度などを測定します。
臭気測定の重要ポイント:複数回測定する!
製造工程の排気では、ニオイの強さが大きく変動する、という点に注意が必要です。
臭気サンプリング(ニオイ採取)のタイミングでたまたまニオイが強い(あるいは弱い)数値が測定され、その測定値に基づいて対策を設計すると、過剰な対策コストの出費や、住民苦情が収まらないという問題発生など、適した対策とならないことが少なくありません。
本件においても、製造工程の情報と照らし合わせながら、複数回、測定を行いました。
その結果、最も臭気の強い値(最大臭気濃度)を確認することができ、その数値を一つの基準として、苦情回避への精度がより高まる対策を検討することができました。
失敗しない臭気測定 のまとめ:
① 人間の鼻を用いて行う『三点比較式臭袋法』により測定を行う。
(成分濃度測定/単ガスppm測定よりも苦情解決に対し適した影響度評価といえる)
② 複数回に分けてサンプリングし、ニオイ排出状況を的確に把握する
③ 苦情回避のカギとなる、臭気ピークを模索する
![]() |
![]() |
サンプリングした臭気 | 臭気測定の様子 |
2.苦情回避の設計案その1:局所排気
臭気測定の結果、
- 既工場における排気方法(製造工程の建屋全体を有圧扇で換気)では、工場敷地外の周辺エリアで臭気が強いレベルで広がってしまう、
- 移転先で同様の排気方法を行えば、周辺住民から悪臭苦情が発生する可能性が高い
ことが確認されました。
そこで解決方法の1つ目として提案したのが、「局所排気」です。
臭気が発生しているエリア(局所)において、臭気発生直後のガスを、周囲へ漏れ出ないように集中的に捕集します。
局所排気を行うことで、悪臭が建屋全体に広がり、さらに建屋から屋外へ漏れ出るのを防ぐことができます。
「強いニオイ」を「集中的に」「漏れ出ることなく集めて」排気するのが局所排気です。
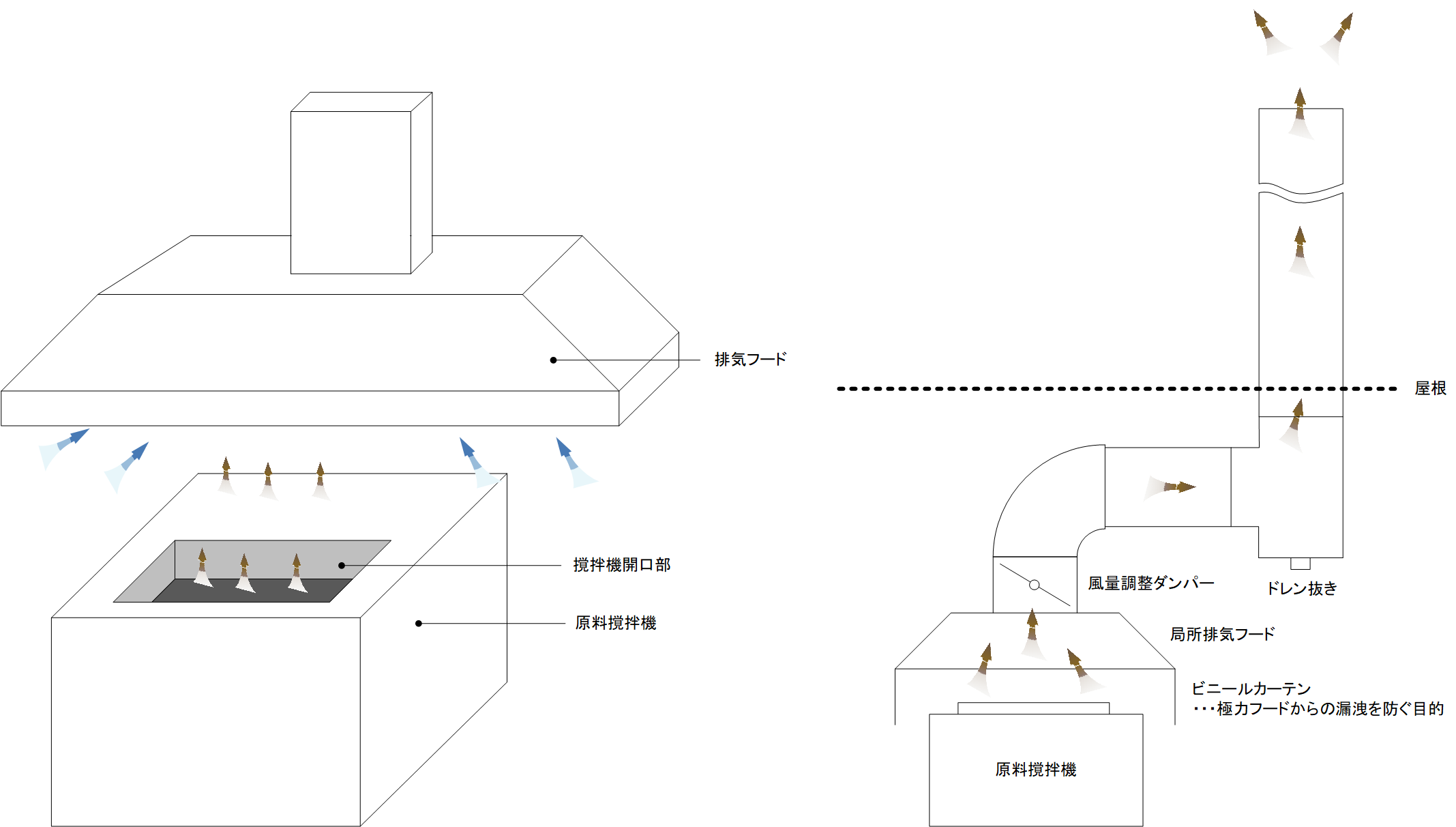
3.排気口の臭気レベルを予想算出
現工場では、建屋からの漏洩+有圧扇での換気によりニオイが屋外に排出されている状態ですが、局所排気を導入することにより、対象臭気をまとめて排気する方法に変更されます。
建屋周辺に漏れ出るニオイが無くなる代わりに、排気口におけるニオイのレベル(排気口の臭気濃度)が、工場周辺への影響度=悪臭苦情発生の可能性を予測するために重要なポイントとなります。
しかし、現状では既工場に排気設備が備わっていないため、排気口の臭気レベルが測定できません。
そこで、発生源の臭気濃度と局所排気の想定風量から、排気口における臭気濃度を予測算出しました。
原料撹拌機から発生する 強いニオイ |
+ |
局所排気で吸引される 周りの空気(希釈エアー) |
= |
排気口の 臭気レベル |
具体的には本件においては、【原料撹拌機からのガス発生量】と【局所排気装置の吸引風量】との比から希釈度を決め、そこから排気口の臭気濃度を予想算出しました。
各工程の予想排出臭気濃度
検体No. | 検体名 | 予想排出臭気濃度 | 予想排出臭気指数 |
1 | 原理用投入時 | 105 | 20 |
2 | 攪拌時 | 1050 | 30 |
3 | C工程 | 83 | 19 |
4 | D工程 | 5250 | 37 |
5 | 蒸気発生時 | 1680 | 32 |
算出の結果、D工程において予想排出臭気濃度が最も強いという予想を得ました。
そこで、この工程の排出臭気濃度を対策ターゲットの主軸とし、この条件においていかに周辺悪臭苦情を回避するか、という対策案を検討いたしました。
4.拡散シミュレーションと、設計案その2
カルモアには、「排気口の臭気が工場周辺エリアにいかに影響を及ぼすか」をシミュレーションする技術があります。
におい対策を導入する前に効果を予測することができるため、対策方法の有効性の判断や、悪臭苦情を確実に達成する計画立案などに非常に役に立ちます。
本件も、前項で算出された排気口の予想排出臭気濃度を使い、排出条件を変動させて、臭気拡散シミュレーションを実施しました。
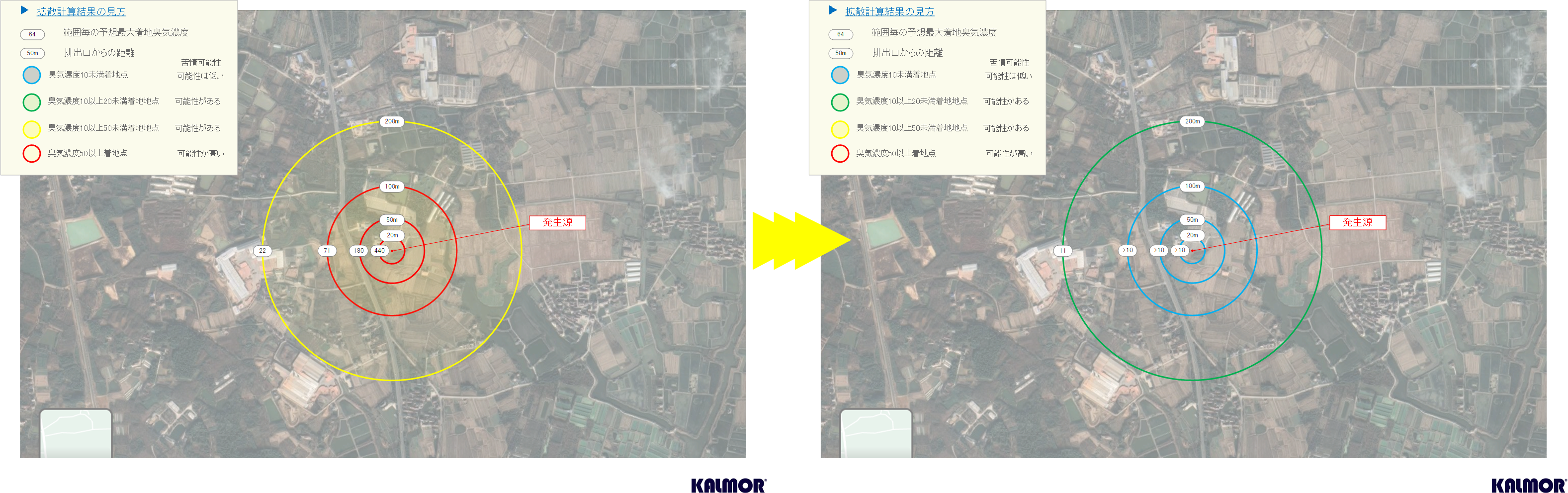
シミュレーションの結果、排出方法を工夫することにより悪臭苦情発生のリスクは限りなく抑えられることが確認できました。
そこで、最も低コストで実施できる対策案として、以下の2つをご提案しました。
【対策1】排出方法の工夫(排気ダクトの設計)を行う。
【対策2】苦情が発生した場合は、消臭剤噴霧装置を導入する。
【対策1】排気ダクト設計の工夫:
より悪臭苦情が抑制できる工夫を施した設計で、排気ダクトを設計・製造します。
この対策のみで苦情を押さえることができれば、脱臭装置を設置する必要がないため、非常に低コストで対策を実現できます。
【対策2】保険としての脱臭装置準備:
工場移転および製造工程稼働開始後、万一【対策1】の効果だけで不十分であった場合には、消臭剤噴霧装置を導入します。
途中からの導入でも無理がないように、設置スペースやユーティリティ準備などを設計段階で仮予定として盛り込んでおけば、稼働後の導入でも最小限のコストで実施できます。
移転後(5年経過)、苦情ゼロを達成!
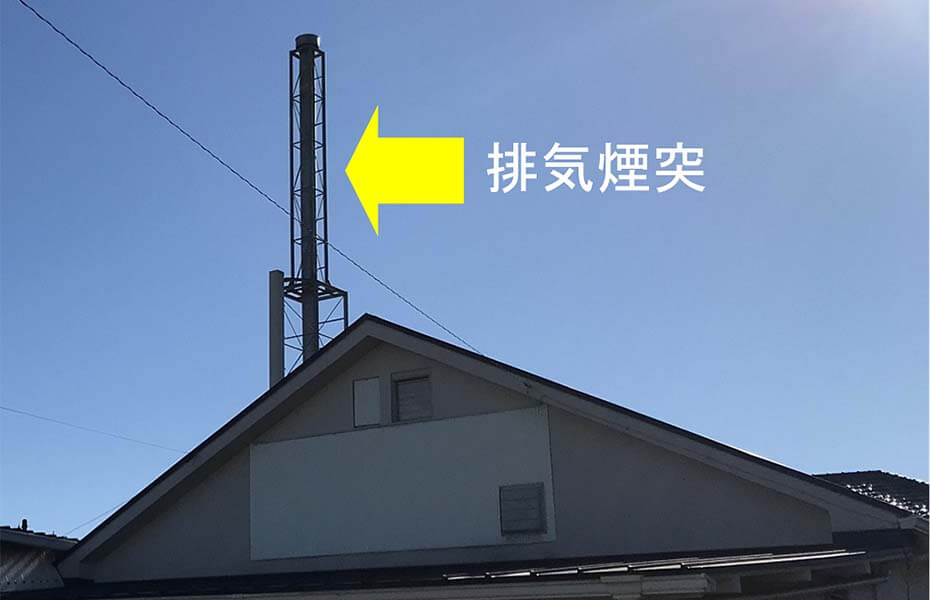
工場移転後、5年経過時点において、悪臭苦情は一切発生しておりません。
苦情が発生しなかったため、【対策2】の消臭剤噴霧装置を導入する必要は発生せず、排気ダクトの設計工夫のみで対策が完了しました。
脱臭装置のランニングコストも発生せず、掛かった費用は局所排気装置とダクト工事費用のみです。
最低限のコストで高い効果を発揮する事が出来、お客様に大変喜んで頂きました。
|
|
撹拌機と局所排気の様子 | 撹拌機と局所排気の様子 |
まとめ
今回は新設工場での、臭気対策事例をご紹介いたしました。
臭気の測定と拡散シミュレーションを実施する事で、最適かつ確実に効果を得る対策案をご提案することができ、苦情を解決することができました。
結果として、局所排気装置とダクト工事費のみで臭気対策を完了する事ができたため、対策費用も大きく削減する事に成功しました。
ニオイにお悩みの際は、ぜひ一度プロにご相談くださいませ。
ご参考ページ:
導入製品・サービスについて
お客様の臭気問題を、調査から対策まできっちりと確実に導くお手伝いをさせていただきます。
人間の嗅覚によって臭気を測定するもので、いくつかの物質が混ざり合った複合臭を判定することできます。
小~大風量・低~中濃度臭気対策に最適な、消臭剤マイクロゲルの特徴を最大限に生かした脱臭装置です。
圧倒的な消臭能力とコストパフォーマンスにより、各種産業工場で大きな支持を集めている【マイクロゲル】。2002年発売以来日本のみならず世界11か国での使用実績を誇ります。
敷地境界での臭気状況をモニタリングできる、定点式のニオイセンサー【LIMOS】。屋内に設置した親機にて、敷地内の臭気を一括して管理できます。
カルモアが独自開発したシミュレーションソフト「KaLmoSカルモス」は、においシミュレーター(環境省配布)をはるかに超える精度と現実性で、悪臭苦情の回避・解決、無駄と失敗のない脱臭装置の設計、悪臭防止法の規制対応を実現します。